Client Description
Our client is a leading precision electronic components manufacturer, specializing in the production of high-tech components for various industries. The company operates in a highly controlled environment where maintaining stringent cleanroom standards is essential to ensure the quality of their products. Due to increasing demand and aging equipment, their existing high-efficiency filters were no longer meeting the required standards, affecting production efficiency and product quality.
Challenges/Pain Points
The primary challenge faced by the manufacturer was the decline in the performance of their existing high-efficiency filters, which failed to maintain the necessary cleanliness standards in their production environment. This led to several critical issues:
- Poor air quality resulting in the contamination of electronic components during production, which ultimately impacted product quality.
- High replacement costs due to the need for frequent maintenance and replacement of the aging filters.
- Difficulty in finding filters that could meet the exact cleanliness requirements, especially as the production scale continued to increase.
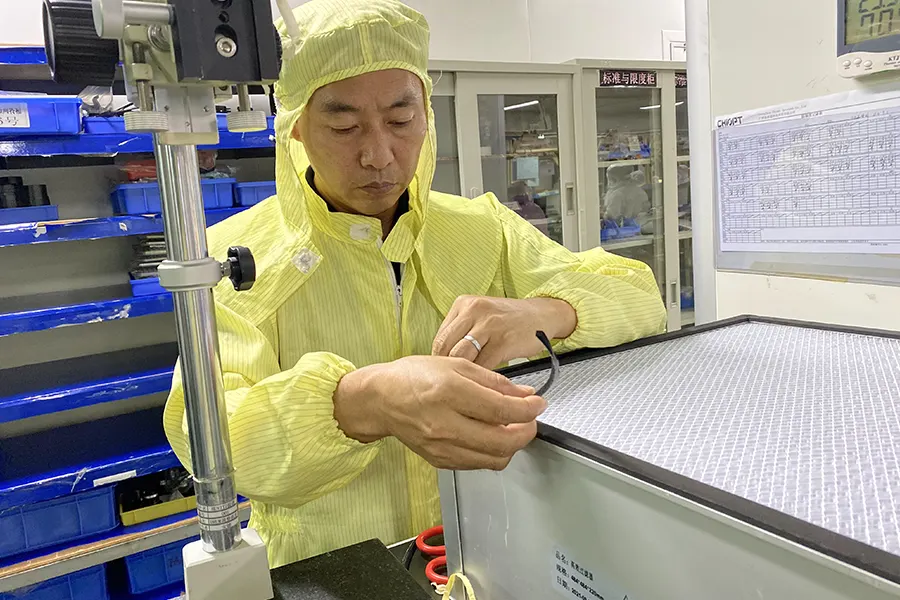
Solution & Execution Steps
To address the client’s challenges, we took a step-by-step approach to identify and implement an optimal solution:
- Cleanliness Requirement Analysis: Our team worked closely with the client’s technical staff to understand their specific cleanliness requirements, conducting a detailed assessment of their production environment and aligning it with industry standards.
- Recommendation of High-Efficiency Filters: Based on the findings, we recommended our high-efficiency filters, designed with ultra-fine fiberglass filter media, which are known for their high filtration efficiency, low resistance, and long service life. These filters are specifically designed to capture even the smallest airborne particles, ensuring the clean environment needed for precision electronics manufacturing.
- Installation, Testing, and Calibration: We provided professional installation and calibration services. Our technicians installed the filters, tested their performance, and verified that the air quality and cleanliness levels met the manufacturer’s strict standards for a clean production environment.

Client Feedback
The client expressed their satisfaction with the solution provided, highlighting several key benefits:
- Enhanced Cleanliness: The new high-efficiency filters significantly improved the air quality in their production facility, reducing contamination risks and meeting their cleanliness standards.
- Cost Savings: The longer lifespan and lower maintenance costs of the new filters helped reduce the overall cost of operation.
- Increased Production Efficiency: With the air quality stabilized, the client reported an improvement in production efficiency, and a noticeable reduction in defects, resulting in higher product quality and customer satisfaction.
The client appreciated our proactive support, thorough analysis, and the ability to execute a seamless transition to a more efficient filtration system that directly addressed their needs.